Having a 100-amp sub panel installed in your home is an important step in properly powering your home. However, with the myriad of electrical wiring options available, it can be overwhelming to choose the right size aluminum wire.
The wire gauge for a 100 ampere subpanel is #2 AWG for aluminum wires. But this answer may change if the length of your cable is too long. It may also depend on the load you choose to put on the wires.
This article will explain what size aluminum wire is necessary for a 100-amp sub panel, so you can make an informed decision. With the right wire, you can ensure that your home has safe and reliable power.
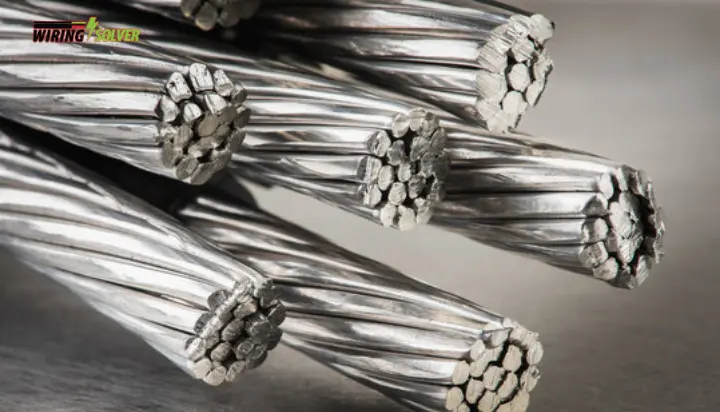
Wire Size Calculator
Enter the load (in watts):
Enter the voltage (in volts):
Enter the distance (in feet):
Select the wire material:
Select the number of phases:
Result:
Why is AWG and Why Is It So Important?
AWG is an acronym for American Wire Gauge. According to American standards, wires are classed based on their current capacity and length.
There are numerous gauge values for cables. The current capacity and the gauge number have an inverse relationship. Because a 6 AWG wire is thicker than an 8 AWG wire, it has more capacity and efficiency.
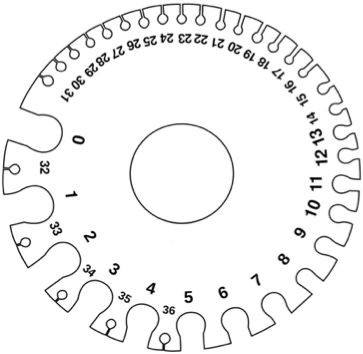
In the above diagram (Fig 1), we can see a calculator for the wire gauges in AWG. We can see that #0 is the thickest gauge and #36 is the thinnest gauge on the calculator.
If you intend to transfer electricity over a greater distance, you need a thicker wire. For example, what size wire is needed to run a 500 feet power supply? Since the distance is very long, you would need a very thick wire.
Using a thinner wire than the recommended gauge is highly advised against. It could result in the wire melting down and even in some worst cases, fire hazards.
What Gauge Wire Should You Use for a Sub Panel?
The answer will vary based on the amperage, material, and length of the cable. But for a 100-amp subpanel, #2 AWG aluminum wires are required. Let’s take a look at the chart below which goes deeper into the gauge requirements.
Amperage Ratings VS Aluminum Wire Gauge Chart (in AWG)
Current | Aluminum Wire |
20 amps | 12 AWG |
30 amps | 10 AWG |
40 amps | 8 AWG |
50 amps | 6 AWG |
100 amps | 2 AWG |
As can be seen from the above panel, as the amperage increases, so does the thickness of the aluminum wire. Which means a smaller gauge.
The appropriate wire gauge for a sub panel dealing with 100-amps is #2 AWG for aluminum cables. However, if you wanted to transfer 50-amps at 150 feet, a thinner wire would suffice.
Using a #2 AWG aluminum wire will ensure the proper flow of electricity from the main panel to the sub panel. Given that the sub panel is not very distant from the main panel, it will not generate much heat.
Aluminum is also lighter than copper. 70% lighter to be exact. But it is also less conductive than copper. It is only 61% as conductive as copper. But over short distances and high amperages, it should not matter much.
How Does the Wire Gauge and Length Affect the Circuit?
There are several factors that can be affected by the gauge of the wire and its length. Such as voltage drops, heat generation, etc.
I will discuss some of the effects of wire gauge and length on the circuit below:
Heat Generation
When current flows through a conductor, heat energy is generated in the conductor. This heat generation is dependent on a few factors. Especially resistance. More resistance means more heat.
Voltage Drops
The longer the wire, the more voltage drop the circuit will face. As electricity has to travel a longer distance, it gets weaker with time.
Thus voltage drops occur. Also the material matters as well. Copper is way more conductive than aluminum. Thus copper will face fewer voltage drops than aluminum.
Line Loss
The line loss in a wire is determined by the wire length, diameter, and current flowing through it. Larger wires offer lower resistance and can carry more power with fewer losses.
If the quantity of power carried is minimal or the wire is not very long, losses in smaller wires remain low.
Wire Resistance
The longer a wire, the more resistant it becomes. This means that it becomes harder for electricity to pass through it. Which in turn increases heat.
On the other hand, a shorted wire means less resistance is provided by the wire. This minimizes the heat which is generated.
Performance of Inductance Loops
The reality is that wire gauge has an impact on inductance loop performance, which has been extensively proven in the traffic business.
When comparing huge loops or loops with extended lead-in lengths, the difference in performance is immediately visible.
Cost
Oftentimes an overlooked sector. The thicker and longer the wire, the more it will cost. As the mass of the conductive metal is increased with its diameter and length.
Aluminum wires tend to cost way less than copper. Almost as half as copper wires.
These are some of the common factors which can be affected by your choice of wire gauge, material, and length.
Summary
A 100-amp sub panel is an important part of properly powering your home, and it is essential to select the right size aluminum wire. The size of aluminum wire you need depends on the length of the wire, the circuit breaker size, and the temperature rating of the wire.
By following these guidelines, you can select the right aluminum wire for your 100-amp sub panel, ensuring that your home is properly powered. With the right wire, you can ensure the safety of your home and its occupants.