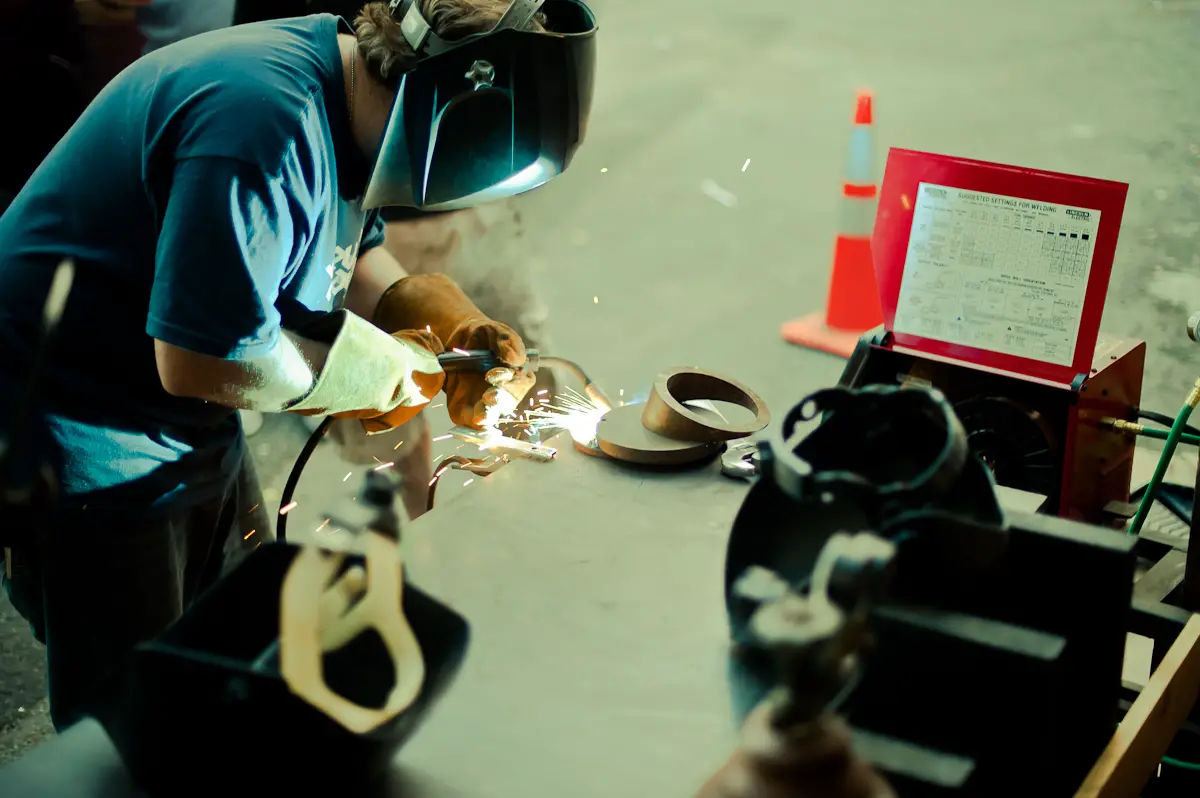
Short Answer
A 3000 to 4000 watt inverter generator should work in most cases but you may want 8000 watts or more for many reasons. One that could work is the AIVOLT 8000 Watts Dual Fuel Portable Inverter Generator. To find out more and if this size will work for you checkout our information below.
Whether you’re a seasoned welder or just starting out, understanding the power requirements of your welding machine and the appropriate generator size is crucial for efficient and uninterrupted work. In this guide, we’ll dive into the intricacies of generator selection for a 140-amp welding machine, considering various factors such as inverter welders, power tools, duty cycles, and more. We’ll explore the relationship between welding machines and portable generators, shedding light on how to make the right choice for your specific needs.
Understanding the Basics: Welding Machines and Power Requirements
Welding machines come in various types, including stick welders, MIG welders, and TIG welders, each with distinct power demands. For a 140-amp welder, you’re dealing with a relatively small welder, but the power it requires is nothing to underestimate. The first step is to locate the welder’s data plate or information label, which provides crucial details about its power requirements, including input voltage, input amps, and maximum amps.
Power Output and Duty Cycle: Key Considerations
Before delving into generator sizes, it’s essential to comprehend the welding machine’s power output and duty cycle. The power output of a welder is usually measured in watts or kilovolt-amperes (kVA), while the duty cycle indicates the percentage of time a welder can operate within a 10-minute period. For instance, the Lincoln Electric LE31MP MIG Welder has a 60% duty cycle so it can weld for 6 minutes out of every 10-minute interval.
More on Duty Cycle
The duty cycle of a welding machine is a critical specification that indicates the percentage of time a welder can be operated at its maximum rated output without overheating. It’s usually expressed as a ratio, such as 20% or 60%, and is followed by the amount of time within a 10-minute period.
For example, if you have a welding machine with a duty cycle of 60% at 200 amps, it means that you can weld at 200 amps for 6 minutes out of every 10-minute cycle. The remaining 4 minutes are meant for the welder to cool down and prevent overheating. It’s important to note that the duty cycle is inversely proportional to the output current. In other words, as you increase the welding current, the duty cycle decreases, and as you decrease the current, the duty cycle increases.
Here are a few more examples to illustrate the concept:
Example: 40% Duty Cycle at 250 Amps Duty Cycle: 40% at 140 amps Run Time: You can weld at 140 amps for 4 minutes out of every 10-minute cycle, with 6 minutes of cooling time. Example: 80% Duty Cycle at 160 Amps Duty Cycle: 80% at 160 amps Run Time: You can weld at 160 amps for 8 minutes out of every 10-minute cycle, with 2 minutes of cooling time. Example: 100% Duty Cycle at 100 Amps Duty Cycle: 100% at 100 amps Run Time: This scenario implies that the welder can operate continuously at 100 amps without the need for cooling breaks within the 10-minute cycle. Example: 30% Duty Cycle at 300 Amps Duty Cycle: 30% at 300 amps Run Time: You can weld at 300 amps for 3 minutes out of every 10-minute cycle, with 7 minutes of cooling time.
It’s crucial to understand the duty cycle of your welding machine to prevent it from overheating and potentially causing damage. Exceeding the duty cycle consistently can lead to reduced equipment lifespan and poor weld quality due to overheating. On the other hand, adhering to the duty cycle ensures that your welding machine operates optimally and maintains consistent performance over time.
Keep in mind that different welding processes (e.g., stick welding, MIG welding, TIG welding) and different welding machines can have varying duty cycle specifications. As you consider your welding projects, be sure to factor in the duty cycle of your welder to ensure efficient and safe operation.
Calculating Power Requirements
To determine the suitable size of the generator, you need to consider the peak power requirements of your welding machine. While the welder’s output may be 140 amps, you need to account for factors such as the type of welding (stick welding, MIG welding, etc.), the thickness of materials being welded, and the use of extra tools. Thicker materials and additional power tools may require brief spikes in power consumption. In the following examples we will show some different materaisl so you can get an idea of what size welder is required so that if you decided to upgrade from a 140 amp that the generator you select is able to handle the larger machine.
Example 1: Mild Steel Let's say you're working with mild steel, which is a common material in welding projects. The power requirements will depend on the thickness of the steel. Thin Mild Steel (1/8 inch or 3.2 mm): Welding thinner sheets of mild steel requires less heat energy. A 140-amp welder might be sufficient for this thickness. Medium Mild Steel (1/4 inch or 6.4 mm): As the thickness increases, more heat energy is needed to properly penetrate the material. You might need to increase the amperage to around 180-200 amps. Thick Mild Steel (1/2 inch or 12.7 mm): Thicker materials demand even more power. You might need a higher-amperage welder, such as a 250-amp machine, to ensure proper penetration and a strong weld. Example 2: Aluminum Aluminum requires more heat energy due to its higher thermal conductivity. Therefore, you'll likely need more power for aluminum welding compared to steel. Thin Aluminum (1/8 inch or 3.2 mm): Aluminum's high thermal conductivity means you'll need more power. You might need a 200-amp or higher welder for thinner aluminum sheets. Medium Aluminum (1/4 inch or 6.4 mm): Thicker aluminum demands even more heat energy. A 250-amp welder or higher might be necessary. Example 3: Stainless Steel Stainless steel has its own set of characteristics that influence power requirements. Thin Stainless Steel (1/8 inch or 3.2 mm): Similar to mild steel, thinner stainless steel sheets can be welded with a 140-amp welder. Medium Stainless Steel (1/4 inch or 6.4 mm): The higher heat conductivity of stainless steel might require a slight amperage increase, around 160-180 amps. Thick Stainless Steel (1/2 inch or 12.7 mm): Thick stainless steel will need more power. A 200-amp or higher welder could be necessary.
It’s important to note that these examples are general guidelines and can vary based on factors such as the specific alloy of the material, joint design, and welding technique. Additionally, using thicker electrodes or filler metals can influence the power requirements. Always refer to your welding machine’s data plate for recommended settings and consult welding charts provided by electrode or wire manufacturers for more precise guidance.
Understanding how the power requirements change with different materials and thicknesses ensures that you select the appropriate welding parameters and use a generator that can provide the necessary power for optimal weld quality.
Selecting the Right Generator Size
Now that you have a grasp of your welder’s power requirements, it’s time to choose an appropriate generator size. Inverter generators are often recommended for welding machines due to their clean power output, low total harmonic distortion, and adaptability to various power levels. They’re particularly useful when working with sensitive electronics and power tools.
For a 140-amp welder, a generator with a wattage rating between 3000 to 4000 watts should suffice for most tasks. However, you may want something 8000 watts and above to be sure you can handle the surges of current and possibly give you some room to upgrade in the future, like the GENMAX Portable Inverter Generator. What ever you decide be sure to take into account the initial surge watt rating required to start the welder and the running watts needed to maintain its operation. Keep in mind that using a generator at its full capacity for prolonged periods can lead to wear and potentially affect the welder’s performance.
Type of Generator: Inverter vs. Conventional
Inverter generators offer several advantages over conventional generators. They provide clean power, low total harmonic distortion, and better fuel efficiency. This is crucial for welding machines, as dirty power with high voltage fluctuations can damage electronic components and disrupt the welding process. Conventional generators are generally less expensive, but they might not deliver the same level of stability and performance as inverter generators.
Special Considerations: Remote Locations and High Altitudes
If your welding tasks take you to remote locations or high altitudes, additional factors come into play. At higher altitudes, engines tend to produce less power due to reduced air density. Some generators offer high-altitude kits to compensate for this loss and ensure consistent power output. Moreover, if you’re working in remote areas, a generator with a longer run time and a larger fuel tank might be essential to avoid frequent refueling.
Noise Level and Environmental Impact
Noise levels are often a concern, especially when working in residential areas or noise-sensitive environments. Inverter generators are known for their quieter operation compared to conventional generators, making them a preferable choice for work areas where noise reduction is crucial. Additionally, consider the environmental impact of your generator. Many inverter generators are designed to be more fuel-efficient, producing fewer emissions and reducing your carbon footprint.
Ensuring Uninterrupted Power Supply
Welding jobs require a stable and uninterrupted power supply. A generator’s ability to deliver consistent power is crucial to prevent interruptions in the welding process. Sudden power drops or fluctuations can lead to poor weld quality and even damage the welding machine. Opting for a generator with higher surge watt capabilities than the welder’s maximum watts can provide an added layer of safety and ensure uninterrupted operation.
Wrapping it up
Choosing the right generator size for your 140-amp welder involves considering a multitude of factors, from the type of welding you’ll be doing to the power requirements of your tools and the specific conditions of your work area. Inverter generators, with their clean power output and adaptability, are often the preferred choice for welding applications. Remember, a generator that’s too small might not provide enough power, while one that’s too large could lead to unnecessary expenses and inefficiencies. By understanding your welder’s power needs and the capabilities of different generators, you can make an informed decision that ensures optimal performance and seamless welding operations.